INDUSTRY 4.0 IN METAL SECTOR
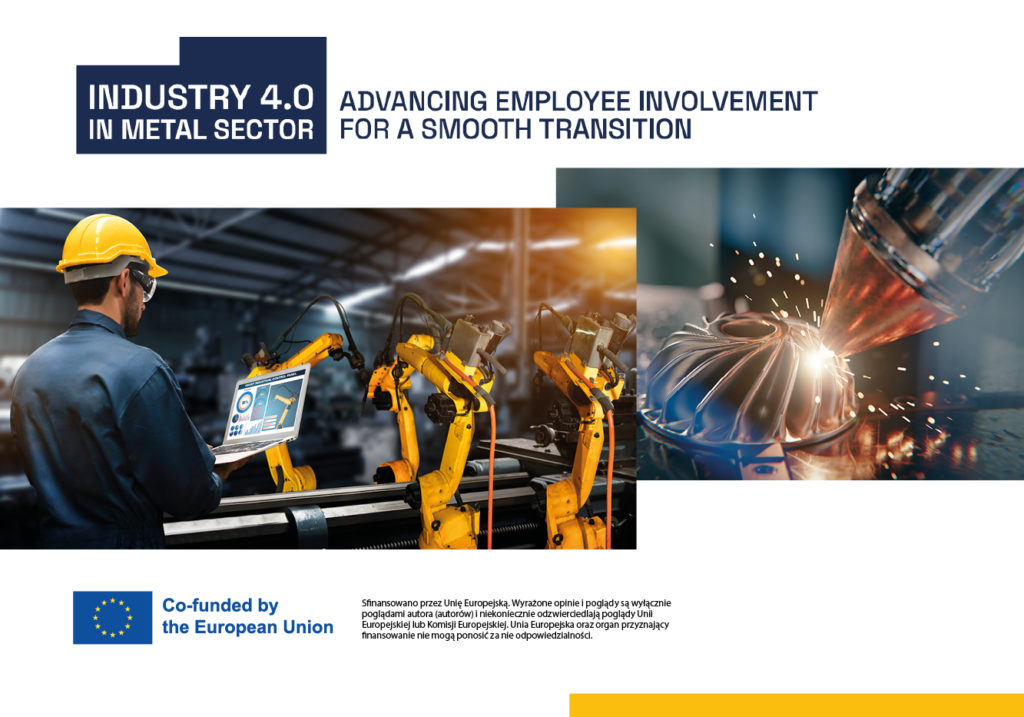
IMS – advancing employee and workers involvement
IMS Industry 4.0 in Metal Sector – advancing employee involvement for a smooth is being implemented from October 2022. The project is financed by the European Union, and representatives of the social partners participate in it from 4 EUMSs (Bulgaria, Poland, Portugal, Romania) and 2 Candidate Countries (North Macedonia, Montenegro). IMS project targets both – employers and employee representatives from the metal sector from six partner countries. Through participating in the project, the target groups will acquire the knowledge of participatory techniques, skills, and information about how to exercise their right. The exchange of good practices will make it possible to strengthen the capacities of social partners on the way to the sustainable development of a Europe that will be more digital, more favorable for the environment and more resistant to crises.
To achieve the goal of the project – the topic of the industry 4.0 – advancing employee involvement for a smooth transition is observed in general but through case studies of six countries in the metal industry.
The metals industry is under intense pressure to transform from an environmental, political, and cultural perspective. A new view of the company’s business implies ambitious goals for energy management and emission control, increased productivity, uptime, better operational cost control, and optimized capacity. The implementation of Industry 4.0 has set new requirements for employees and management. New ways of working, its organization, the emergence of non-standard forms of employment, requirements for a dynamic workforce require all actors to engage, cooperate with each other and bring optimal solutions. All this requires increased engagement and interaction of all actors. Informing and consulting and achieving a dialogue that results in joint decision-making is considered a win-win combination for better business and better working conditions.
Although there are differences in the economic and social development of the countries participating in the Project comparative overview of strategic and legislative solutions at the national level in the six countries showed – All countries have more or less harmonized their legislation with EU legislation. They have been advancing in their digitalization efforts but still struggle to close the gaps in digital skills and the digital transformation of SMEs.
There are numerous positive effects of the introduction of automation and digitization – better productivity, easier handling of heavy machines, better safety at work, cleaner jobs, reduced number of errors and scraps and greater competitiveness. The risks were also pointed out – de-professionalization, increased monitoring, social exclusion, as well as the lack of qualified labor force, and the increasing pressure that employees in this sector feel – increased demands and enormous responsibility.
The SWOT analysis:
Strengths | Weaknesses |
• the EU related to this area. • The strategic framework clearly recognizes the importance of employees’ involvement and benefits to the digital transformation. • There is a willingness The legal framework in all the countries is harmonized with the legal acquis of both sides, employers, and unions, to cooperate with each other and jointly solve problems in the interest of a smooth digital transition. • All actors at the company level are aware of the positive effects of the introduction of automation | • There is no obligation to inform and consult employees. Laws are not respected. • There are no trade unions in the small and medium-sized enterprises that make up a significant part of the structure of the metal industry in the given countries.• Social exclusion makes communication, information, and consultation difficult.• Lack of motivation at the workplace reduces interest in participating in company activities.• Lack of involvement of employee representatives in the initial stages of digital transformation |
Opportunities | Threats |
• The recommendations of European trade union and employer federations on the importance of social dialogue • Involvement in regional and European projects and the exchange of experiences contribute to a better knowledge of the problems and practice of social dialogue and the use of the right to information and consultation at the company level.; The exchange of good practices encourages and equips employees and employers | • The greatest threat to any aspect of workers’ ability to influence is the ever-decreasing rate of unionization. • The introduction of technology in production processes in statements in collective agreements is treated vaguely. • Labor demand caused by digital transformation tends to favor more highly skilled profiles and can lead to establishment of fractions and divisions, lack of cooperation between WCs and trade unions and other representatives of employees |
Within the Project, were created manual and action plan. The IMS Manual will map the key stakeholders and present their role in advancing the workers,’ employees’ participation in the decisions made at the company level. “Employee Participation Action Plan detail is the ways in which the workers,’ employees’ and employers can participate in the decision at the company level regarding the transition to the industry 4.0. Working hours, new skills and overcoming the gap between older more experienced workers and younger workers who have digital skills, new forms of employment, health and safety at work, energy efficiency and environmental protection are certainly issues for a new agenda and innovative solutions. Support, and other stakeholders, such as local communities, the media and the public would certainly not be left out. The conclusion is that the exchange of information, examples of good practices, and the practice of exercising rights and the inclusion of current issues in the social dialogue agenda are especially important.